Rapid Prototyping Using 6 Axis CNC Machining
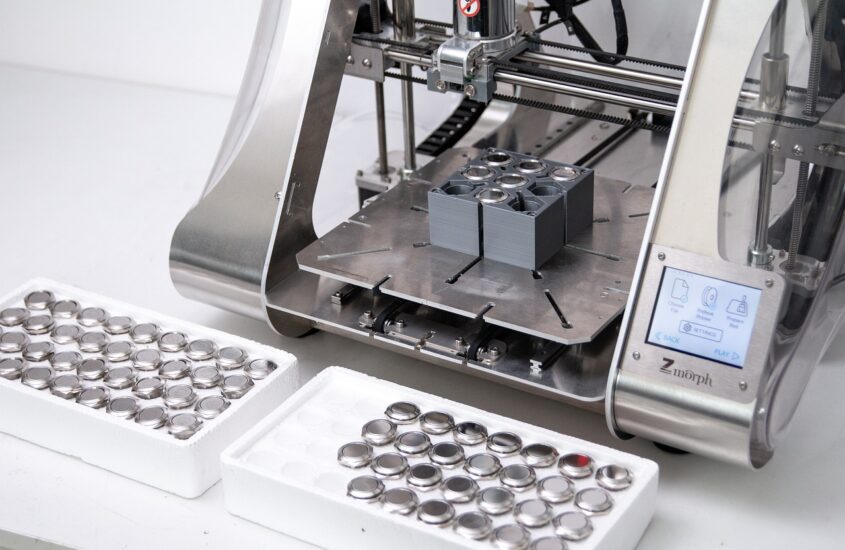
Rapid prototyping is a way to design and develop components and models in a fraction of the time it would take using traditional manufacturing. CNC machining (computer numerical control) is a fairly common subtractive technique for producing custom parts. Before understanding the capabilities and benefits of 6 axis CNC machining, it’s important to compare the advantages and disadvantages of subtractive and additive manufacturing methods to establish which technologies are most appropriate.
Subtractive Versus Additive Manufacturing
There are two main types of ways for rapid prototyping – additive manufacturing and subtractive manufacturing. CNC machining is subtractive. It involves starting with a block of material and carving it down into the shape you want. 3D printing is additive manufacturing, placing layer after layer of material to get the desired product.
Both types of manufacturing expedite the prototyping process. The biggest consideration when selecting a method for your business is to determine the volume and type of material you will be using, which will affect the speed of fabrication. A large object such as a large metal cog is better suited for subtractive manufacturing, whereas a small plastic part, such as a bracket might be best for additive manufacturing.
Additive manufacturing incorporates digital 3D design data to build the prototype by depositing layers of material. It gives original equipment manufacturers (OEMs) across product categories an opportunity to produce models for current or potential customers while saving money on expensive models. OEMs can even prototype new products for customers to explore new product opportunities.
In contrast to additive manufacturing, subtractive manufacturing uses CNC machining to remove material. This means that a 3, 4, 5, or 6 axis CNC machining setup starts with a block of material and cuts out pieces until the prototype is finished. The CNC machine uses replaceable cutters and spinning tools to shape the block of material. This allows the machine to generate great dimensional accuracy across a number of different materials, including metals and plastics.
Rapid Prototyping
Rapid prototyping involves several techniques to fabricate a scale model of a part in a relatively short time. It allows OEMs to ensure their instruments, components, parts, products, and systems are properly designed and engineered and will work together in an integrated, seamless manner. Once a part or component is prototyped, it can be tested to ensure it meets the engineer’s specifications. If anything needs to be adjusted, a new prototype can be developed that incorporates alternative designs in a relatively quick turnaround.
If your company is looking into rapid prototyping, you may want to consider 3D modeling and 6 axis CNC machining options. For companies that operate in industrial environments, ensuring reliability and high performance is paramount. This is where CNC machining shows its true colors. We take a further dive into CNC machining with up to 6 axes and the benefits it brings to industrial-grade prototypes and models.
6 Axis CNC Machining
CNC machining uses standard processes such as milling, turning/lathing and drilling for rapid prototyping. High speed multipurpose vertical machining with 6 continuous axes will typically create movements across the principal X, Y, and Z planes as well 3 rotary axes. The addition of the 6th axis provides greater freedom to the tool movements and transitions, and therefore allows the machine to execute its program with greater speed and efficiency.
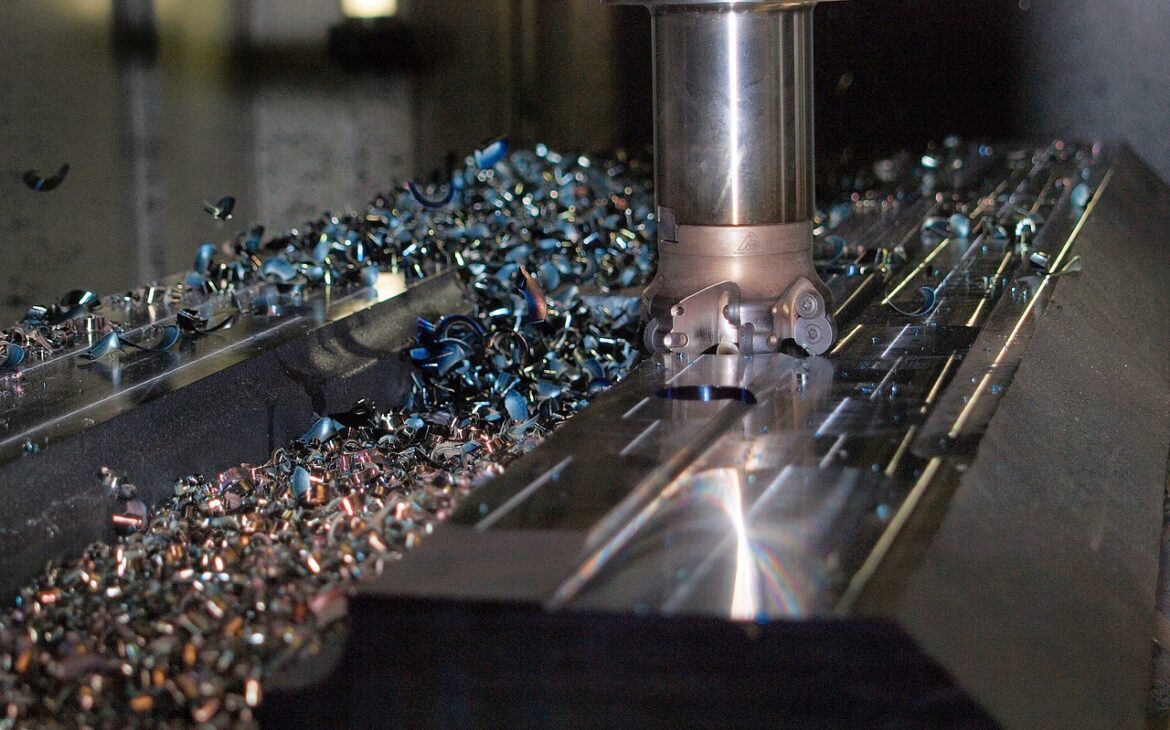
- Applications – When it comes to prototyping, the addition of a 6th axis allows OEMs to tackle complex geometries, like turbines or engine blocks. This is particularly useful for industrial parts that can be particularly expensive if purchased in bulk.
- Benefits – There are several benefits to using 6-axis CNC machining, however, the greatest is often characterized by its fast process. The 6-axis milling can decrease cutting times by as much as 75%. The additional CNC machine axis delivers a greater range of tool movements and transitions with greater speed. This offers a variety of surface finishes that can be smooth, stepped, mottled, etc.
While 6 axis CNC machining is typically more expensive than additive manufacturing, the method is better suited for manufacturing voluminous items and parts, especially if they are metal and designed for industrial uses.
Takeaways from Subtractive Manufacturing
In summary, subtractive manufacturing using 6 axis CNC machining is the favored method for OEMs looking to produce more complex, finished parts and components. The main reasons for this are the speed of the process, the smoother surface finish, and the ability to produce products at a higher volume. The additional axis delivers smoother actuation of the tool head and allows OEMs to take on more complex parts and components.
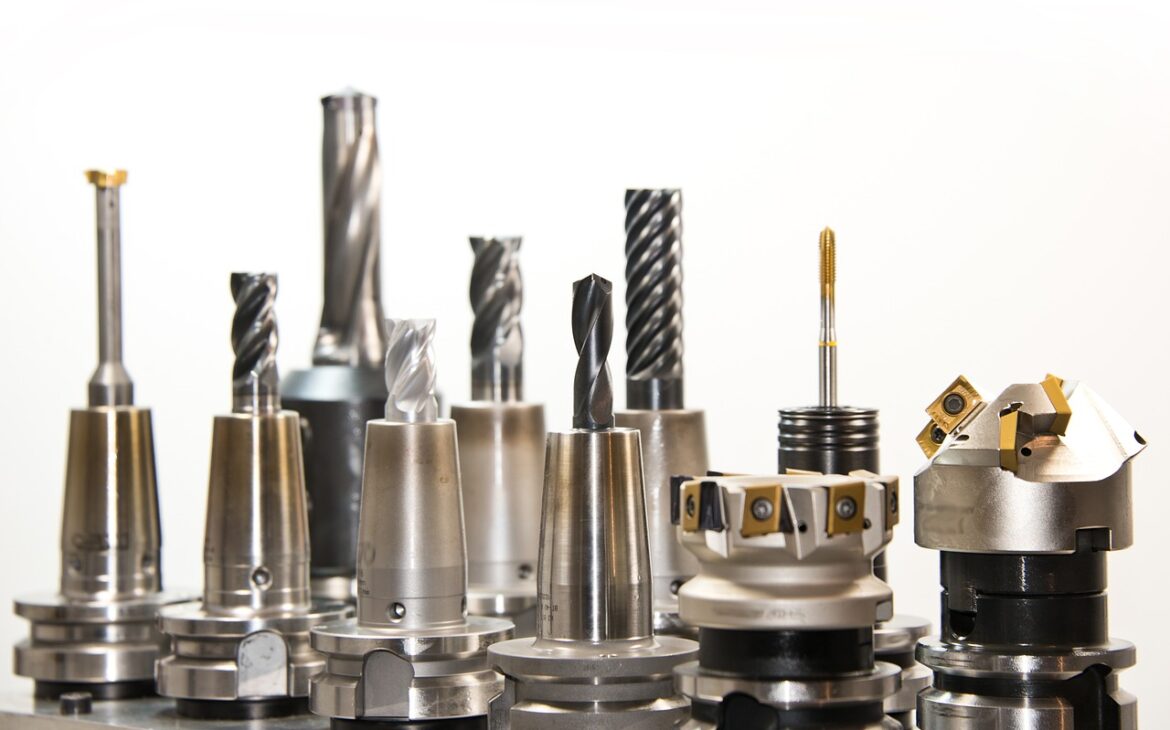
Add to this the fact that CNC machines can work with several industrial-grade materials makes them a perfect option for OEMs that are looking to design replacement parts or additions to existing automation systems.